NWP Employee Spotlight: Rene Gomez
NWP Employee Spotlight Series:
Illuminating Stories from the People of Northwest Pipe
At Northwest Pipe Company, our team members are the foundation of our success, and we take pride in our diverse and talented workforce. This series shares the inspiring stories and career journeys of employees from different departments and locations. In each installment, we interview one of our team members and delve into their experiences, challenges, and accomplishments, and discover why they choose to build their career with Northwest Pipe Company.
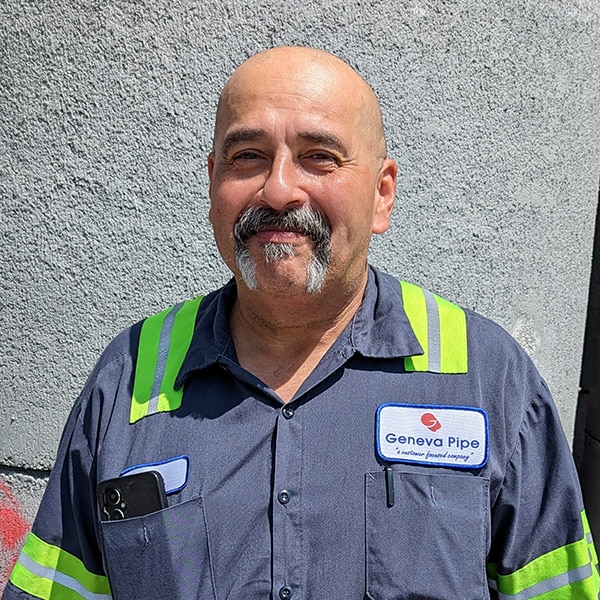
Spotlight on: Rene Gomez
Manhole Machine Operator III – Lead | Orem, UT
As a team lead with Geneva Pipe and Precast, Rene Gomez supervises the Orem Drycast Plant’s second shift, overseeing a team of six employees including laborers and mixer operators who work together to produce high-quality concrete manholes. He’s been with Geneva Pipe and Precast for nearly seven years, and while the work as a manhole machine operator is challenging, Rene finds reward in the teamwork demonstrated by the employees and managers in his department, and in seeing the superior finished products that result from their collaborative efforts.
Looing back at when you first applied, what made you want to join Geneva Pipe and Precast?
I had previous concrete experience—before this, I spent 10 years laying concrete driveways, sidewalks, and building foundations. So, the idea of working in drycast production intrigued me. I was initially hired as a laborer, made my way to back-up manhole machine operator, and then operator. That was all within my first two years. Now, I’m the Second Shift Supervisor.
What are some of your responsibilities as a Drycast Supervisor?
My #1 responsibility is making sure everyone is working safe. I lead a Safety meeting about three times a week, spending 5-10 minutes at the start of the shift focusing on specific topics like proper usage of safety harnesses and ladders, for example. My other focus is production efficiency and quality—ensuring each finished manhole is free of cracks, rocky surfaces, or any other issues that could affect its quality.
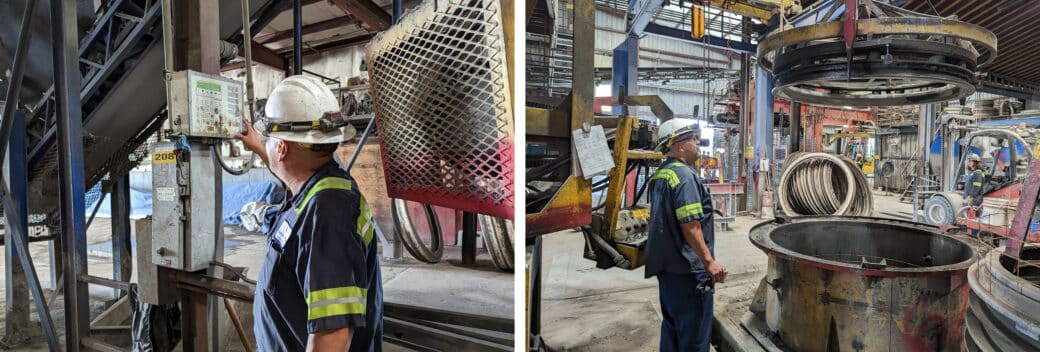
Can you tell us a little more about the manhole manufacturing process?
First, the drycast concrete is mixed and then poured via conveyer belt into the manhole machine form. The machine vibrates to settle and compact the concrete mix, pushing out all the air bubbles and excess moisture. The form is then removed and the manhole is lifted by crane on a metal pallet out of the machine. We brush the top to ensure a smooth finish, stencil the product, and then transfer it via forklift to the steaming area where they are covered and cured overnight.
During our shift, we make on average 35-45 manhole pieces, depending on the size. Our 60-inch diameter cones each take about 10-12 minutes, 48-inch cones take 5-8 minutes, and risers take 5 minutes or so. So, we’re constantly moving. But the manhole machine is the hardest one to run in the whole plant. Other machines are more automated, but in our case, we need to start and stop it on our own, figure out how long to vibrate each piece, and then move each piece to the steaming area.
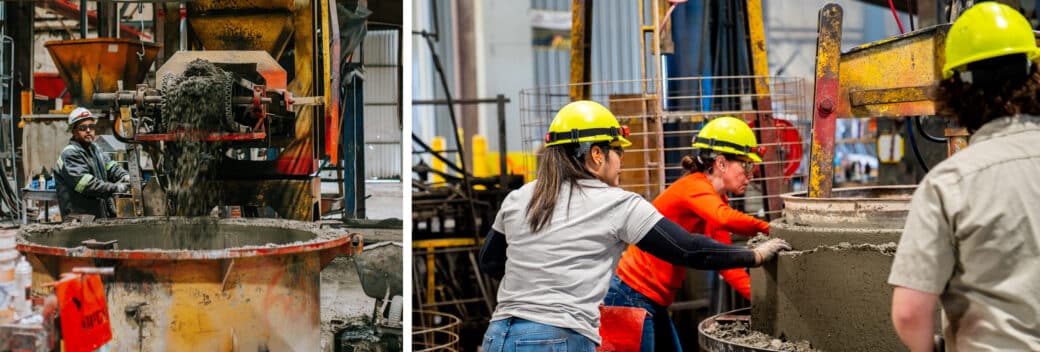
What do you find most rewarding or enjoyable about your job?
Producing a quality product. When I started as a backup manhole machine operator, after the first three runs I did, I got called into the breakroom. Waiting for me there was my supervisor and a couple of UDOT inspectors. The inspectors told me, “We’ve never had manholes that look so good,” and presented me with a gold coin. I’ll never forget that moment. Geneva Pipe has been fulfilling UDOT contracts for many years, and UDOT has very high standards. To receive that level of compliment on my work is a point of pride that continues to motivate me today.
Tell us about your experience in the Navy. What skills did you bring with you into your civilian career?
I spent six years in the Navy stationed in San Diego. During that time, I did tours to Hong Kong, Singapore, and the Pacific Islands. Back then, naval ships were steam-powered, so as a Boiler Technician (BT) I was working on steam propulsion motors. My goal was to become a Third Class BT but I surpassed that goal and was promoted to Second Class. I had other BT’s reporting to me, so that’s where I learned my leadership skills. Doing machinist work and taking apart engines and cranes gave me engineering and maintenance skills that I still use today. If there’s an issue with our manhole machine during our shift, I’m the one who fixes it. I can do just about everything but electrical work.
Which of the Northwest Pipe Company ACT Values (Accountability, Commitment, Teamwork) resonates most for you in your role?
Accountability and Teamwork resonate with me the most. My department is accountable for producing a quality product day in and day out, and the only way we are successful is by working as a team. This is by far the best team that I’ve ever worked with—everyone helps each other out. There’s a good sense of comradery and a strong work ethic that we all share.
What advice do you have for someone starting a career at Geneva Pipe?
My advice is to pay attention, learn the machines, and you can move right up the ladder. That’s not to say that you won’t be challenged; the work is tough. You’re on your feet all day, but you get used to that fast. Cleaning the pit is probably the hardest part of the job as a manhole laborer or operator. Throughout the shift, concrete falls into the pit below the manhole machine. At the end of the day, we have to manually shovel it up into a bucket and jackhammer anything that’s hardened. It’s hot and tiring…you definitely get a good workout! But we work in pairs and take turns, again it’s about Teamwork. So, I guess my other advice would be that no matter what role you’re starting out in, to stick with it. It’s hard work, but it’s a good Company to work for.
After nearly seven years, what makes you want to stay at Geneva Pipe?
I like my job, it’s challenging and exciting. And, again, it’s a good Company to work for—actually, the best I’ve worked for, and I’ve been with maybe eight different companies since I left the Navy in 1985. What makes it different is the values of the Company and the people at the plant. You can go to management with a concern and they do their best to resolve it; they don’t give you a hard time if you need help or ask questions. Everyone is supportive and looks out for one another. Plus, the pay is good.
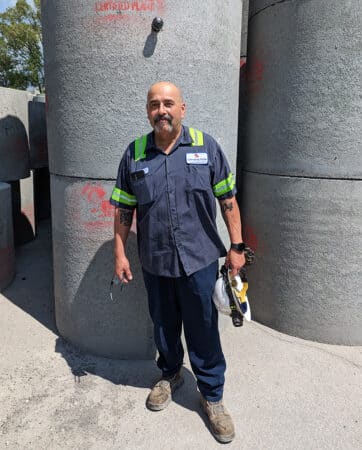
At Geneva Pipe and across Northwest Pipe Company, all employees are encouraged to participate in the process improvement program aimed at reducing waste. What’s an improvement that you or your team has implemented?
About a year ago I suggested that we get radios so that the department supervisor and the lead manhole machine operator could communicate in real-time. Before that, we would have to physically go find each other to give updates or directions, which resulted in wasted time and movement. The radios have improved both communication and efficiency. Plant leadership is very receptive to ideas that help the shift work more efficiently or safely, and these ideas can come from employees in any role, so everyone’s input is valuable.
What do you like to do to unwind after work?
My fiancé and I love to drive up to the mountains, take nature walks, picnic when the weather is warm, and just enjoy the outdoors. I’m from San Diego, so getting to mountains and trees like we have here used to take hours to drive. The nature here just blows me away. We’re getting married in September, so we’ll take advantage of the scenery with an outdoor wedding.
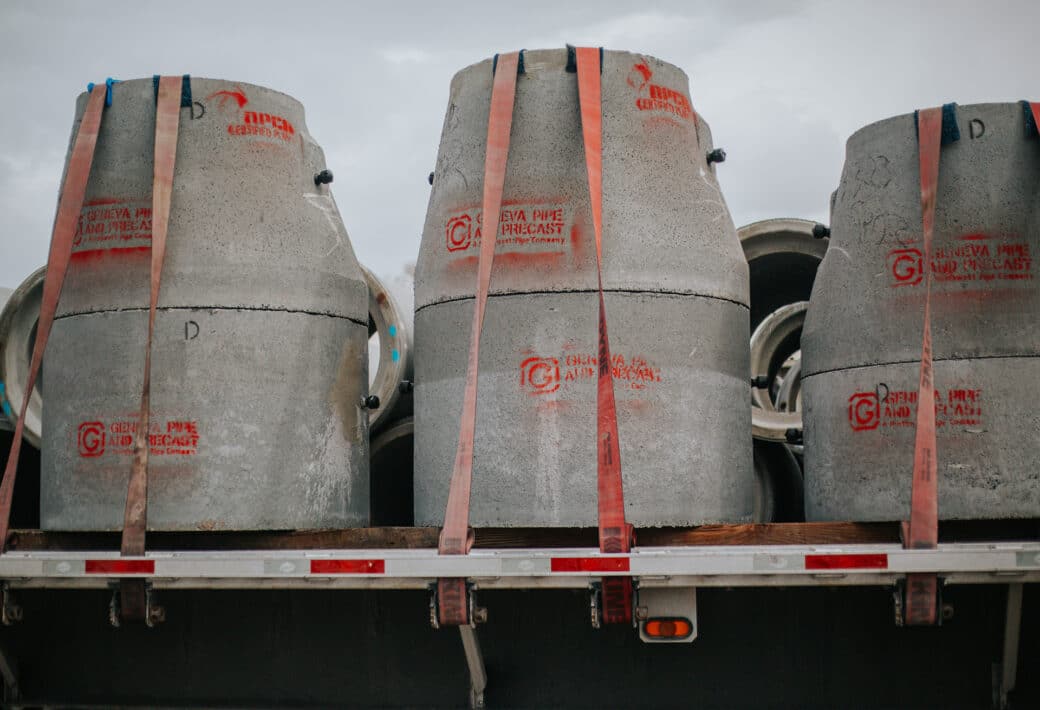