Geneva Pipe’s Hybrid PVC Manhole System Provides Permanent Rehab Solution for Arizona Sewer Project
The easy-to-install method allowed crews to efficiently rehabilitate two manholes in just three days, with no bypass required.
In Surprise, Arizona, an hour northwest of Phoenix, Arizona, Geneva Pipe and Precast partnered with CPM Pipelines to rehabilitate two concrete manholes utilizing our Hybrid PVC Manhole System. These manholes are downstream from a 24-inch force main discharge point, a high-flow area in the sanitary sewer system where caustic hydrogen sulfide (H2S) gases are prevalent. The constant H2S exposure makes these structures particularly susceptible to microbiologically influenced corrosion (MIC), resulting in accelerated concrete decay and severe degradation.
The City of Surprise considered several options for rehabilitating these structures, including epoxy coating. However, given the severity of the degradation, an epoxy coating would only provide a temporary solution with an estimated service life of less than five years. Furthermore, installing epoxy coating involves multiple steps, which may include pressure washing and applying new grout, and can take up to three days for a single manhole.
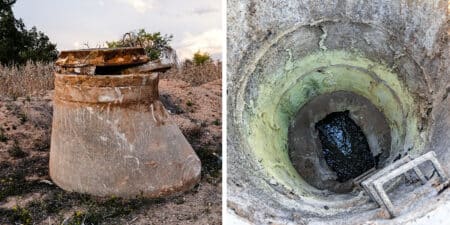
Our Hybrid PVC Manhole System, on the other hand, offers a permanent structural rehabilitation method that can be completed quickly and economically. It was selected as the optimal rehabilitation method for this project for its easy-to-install design, watertight and corrosion-resistant components, and long-lasting performance guarantee, which includes a 50-year warranty against corrosion and 100-year design life.
Project Design & Manufacturing
The project design process begins with scanning the existing structures to create 3D models. The Geneva Pipe and Precast team evaluates these scans to qualify the project for the Hybrid PVC Manhole rehabilitation method. The scans are compared to the original engineering drawings of the existing manholes and used to design the new FRP bases, PVC risers, and lids, which are engineered to fit the existing concrete structures.
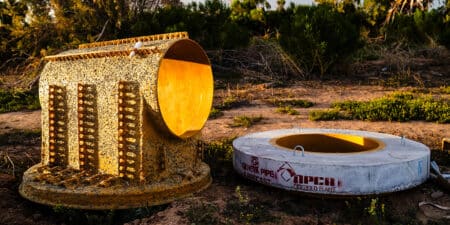
Production of the FRP base for this project involved fabricating a custom EPS foam mold specifically designed to accommodate the existing 48-inch manholes’ channel configurations, which included 24-inch pipe connections. Multiple fiberglass resin layers create a durable plastic shell with a smooth interior finish. The exterior is coated with aggregate, and bonding bridges are added to anchor the base liner in the cement grout during installation. The lid is constructed with steel-reinforced concrete, an integrated FRP liner, and a 24-inch opening. These custom components, along with a 42-inch PVC riser cut to 15 feet in depth, were delivered directly to the job site, ready for a hassle-free installation.
Rapid Rehab, No Bypass Required
Crews from CPM Pipelines efficiently installed both Hybrid PVC Manhole Systems in just three days without interrupting the normal flow of the manholes. The modular design and easily stackable components, customized to fit the contours of the existing manhole structures, enabled crews to complete construction in a live sewer with no bypass or vacuum trucks required. The contractor remarked that the process was “seamless and efficient,” minimizing disruption to the community.
On day one, the first of the old manhole cones was excavated and removed, and by day three, the two new systems were installed and fully operational. CPM Pipelines Project Manager Levi Hawkins, P.E., noted that the process is as fast as, if not faster than, alternative rehab methods, as the Hybrid PVC Manhole components (FRP base, PVC riser, and FRP-lined lid) easily stack into place. The procedure is simple and easy to follow, making it a low-risk rehabilitation solution.
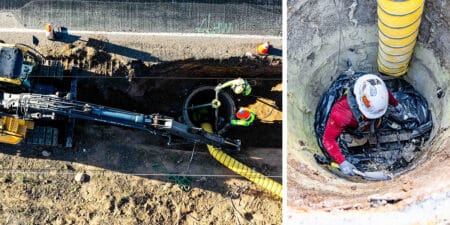
Surface Preparation
The two existing manhole structures were severely corroded, with notable scaling and decay around the interior walls and base channels. Once the cone was removed and an access tripod and fresh air supply were set up, crews safely entered the live sewer to begin surface preparation. They covered the base with plastic sheeting, removed the old ladder steps, and scraped loose substrate from the walls, bench, and invert using handheld and power tools. No pressure washing was required on this project, which helped streamline the rehab process.
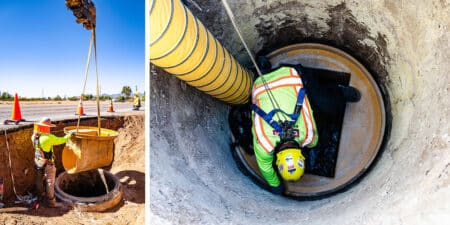
Right: grouting around the new base.
Installing FRP Base and Connectors
After cleaning the interior surfaces, the contractor. then plugged the inlet pipe with an air bladder to halt the wastewater flow, enabling the installation of the FRP base and pipe connectors.
Next, crews lowered and placed the FRP base in between the cut ends of the pipe, leveling it to ensure proper placement and slope angle. Then, the expandable pipe connector was wrapped around an air bladder, saturated with a water-activated expanding resin, and dropped into the manhole, where a crew member carefully positioned it into the inlet pipe end so that it just slightly protruded into the FRP base. The bladder was filled until the stainless steel ratchet device on the inside of the connector fully expanded. Then, the bladder was deflated and removed, leaving the expanded connector securely in place. Crews visually inspected the connector to ensure an airtight seal against the opening of the FRP base and pipe.
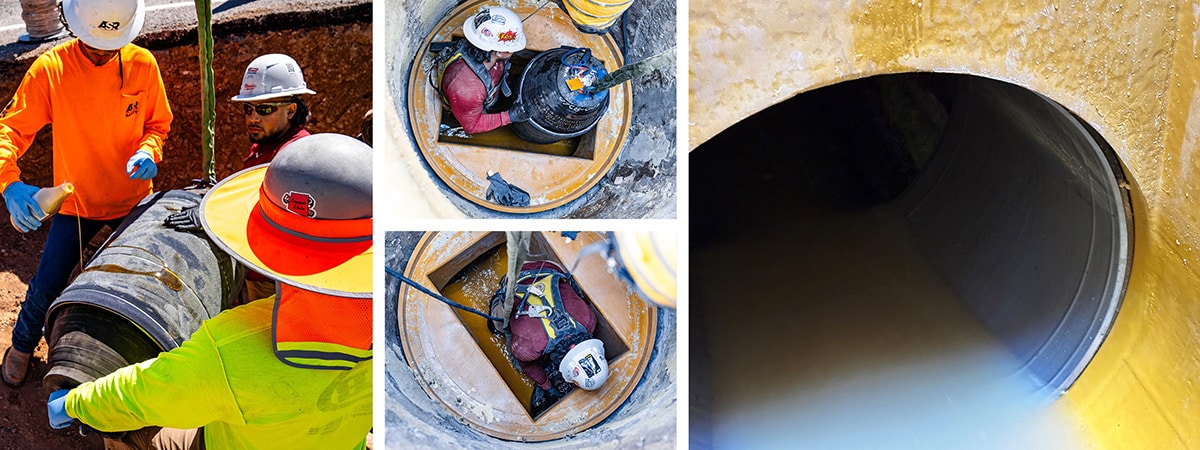
The steps were repeated to complete the outlet pipe connection, followed by grouting of the annular space between the new base liner and the existing manhole base. Finally, the bladder in the inlet pipe was deflated and removed, releasing the flow of wastewater through the newly integrated FRP base liner.
Placing the Riser & Flat Lid
Mastic was applied around the inside of the FRP manhole base liner to accommodate the PVC riser and create a watertight seal between the nested components. The PVC riser was lowered into the existing manhole until it was plumb and the mastic engaged and compressed. Because the PVC riser is installed as a single piece, the system eliminates almost all secondary joints produced when stacking conventional precast risers. Crews then used a ready-mix concrete truck to quickly fill the gap between the PVC riser and the existing concrete manhole.
Mastic was also applied to the top of the PVC manhole riser to seal the lined flat lid in place. After carefully setting the flat lid, ensuring it is centered over the riser and securely sealed, the riser was then backfilled and compacted to the top of the flat lid. A cast iron frame and cover complete the newly rehabbed manhole.
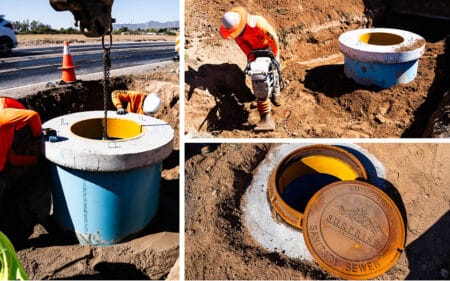
Ensuring Project Success
Members of the Geneva Pipe and Precast engineering team were on hand to offer support during installation and gather feedback from the contractor. The valuable insights gained in the field from the installation crews will help ensure success for future projects using our Hybrid PVC Manhole System.
The two newly rehabilitated manholes not only revitalize deteriorating sanitary sewer infrastructure but also safeguard it for decades to come. Providing enduring protection from corrosion, infiltration, exfiltration, and abrasion, these manhole structures will continue to serve as vital components within the City of Surprise Wastewater System for years to come.